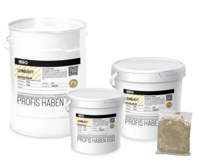
EGO and GLASS, that is a connection that has endured since the company was founded in 1947. It has always been our claim to meet the requirements on one of the most challenging substrates. Due to the multitude of possibilities that have successively developed in the field of glass bonding and sealing, we have always been forced to react. As a result, we are now in a position to offer a comprehensive range that meets all requirements in the field of glass bonding and sealing.
With our partnership with the Rosenheim Institute for Window Technology, we set ourselves the highest quality standards. High-quality applications in the areas of windows, facades, greenhouses or monument protection - that is what we demand of ourselves. Only in this way can we, as a partner of the glazier trade, fulfill the wishes of our loyal customers. Just give us a call, we will be happy to help you find the right product for glass.
The restoration and renovation of historic windows, taking into account the protection of historical monuments as well as sound and heat insulation, is a great challenge which we successfully meet. For this purpose, we have a range of putty products available for the most diverse requirements and, as the manufacturer, we will be happy to assist you with application questions, especially in the area of window glazing. Our putties are also subdivided according to stress groups. You can view these HERE.
Below are the important points in window sealing with putty:
UV adhesives are perfect for glass to glass or glass to metal bonding with fast cycle times because it cures in seconds with UV or daylight.
Self-cleaning surfaces "Lotus effect" (do not use silicone - here only hybrid sealants approved and listed by the glass industry), some powder coatings, formwork oil residues or impregnations
Spectrum and energy of the lamp, distance of the lamp from the glue line, degree of aging of the lamp, layer thickness of the glue, Transmission, absorption and reflection of the glass
The sealing of mullion-transom facades, sloped glazing, such as roof glazing and conservatories.
The compatibility between the silicone sealant and the PVB film must be given and guaranteed. The materials used must not show any negative reactions or interactions and must be compatible with each other.
The film is usually made of polyvinyl butyral - a tear-resistant and elastic Polymer film, which is used as between the glass panes, as well as helps to bind splinters and increase the residual load-bearing capacity.
The sealant must be compatible with the respective insulating glass edge seal, laminated glass (VG) and laminated safety glass (VSG) according to ift guideline DI 02/1. This refers to the contact surfaces in the glass rebate as well as in the flush sealed area.
Yes, for the application we have a liquid, clear addition-curing two-component silicone rubber for glass/glass surface bonding in our range.
CONLOC SK 713 polymerizes without shrinkage in any layer thickness to form a viscoplastic, ageing-, weather- and UV-resistant end product and is suitable for surfaces up to approx. 600mm x 900 mm. The glass surfaces to be bonded must be thinly pretreated with CONLOC Primer SK 713.
Spectrum and energy of the lamp, distance of the lamp to the glue line, degree of aging of the lamp, layer thickness of the adhesive, Transmission, absorption and reflection of the glass
The required irradiation times are between approx. 15 seconds and 5 minutes. However, this depends on various factors such as the spectrum and energy of the lamp, the distance between the lamp and the adhesive joint, the thickness of the glass, the degree of aging of the lamp, the layer thickness of the adhesive, the Transmission, absorption and reflection of the glass, and should always be determined individually for each application by preliminary tests.
Due to the pigmentation, up to 5 times longer irradiation time is required for curing the colored grades CONLOC® UV 665 compared to the colorless setting.
If a higher temperature effect on the adhesive bond is avoided, a longer irradiation time will not have a negative effect.
The substrate or substrates must be UV-permeable. In the case of laminated safety glass, special daylight-curing UV adhesives such as CONLOC® UV 680 and CONLOC® UV 688 are used because of the UV impermeability of the laminated film.
Shaded areas and UV-impermeable materials such as laminated safety glass can also be cured without UV irradiation using CONLOC® UV 683 and the special CONLOC® Activator 953.
UV bonding is almost final. Bonds with UV acrylate adhesives can be released with temperatures around 200 °C due to the thermoplastic property and as far as the components allow. The risk of glass breakage in the event of an uneven supply of heat must be taken into account.
For constructions requiring elastic bonding and large-area bonding of materials with widely differing coefficients of thermal expansion.
Bonds where the bond/adhesive joint is permanently exposed to water, e.g. aquariums!
Permanently high temperature stressed bondings - danger of yellowing.
Nm stands for Nanometer. The UV adhesive polymerizes in a wave range of 320 - 400 nm. The specified light spectrum must be covered by the UV light source. Ultraviolet light is the most energetic part of solar radiation and is divided into the UV ranges A, B and C based on its wavelength. UVA rays have the longest wavelength (315 to 400 nanometers)
Due to the controlled curing and fast curing speed, short cycle times are possible in industrial production.
At least one of the materials must be permeable to the required wavelength. For applications with so-called shadow areas and for bonding laminated safety glass, we have a special UV-curing adhesive with activator in our range.
UV adhesives have a wide range of applications and are suitable, for example, for the manufacture of glass furniture, glassware, acrylic glass, for the optical industry, bonding of fittings/glass, automotive, electronics industry.